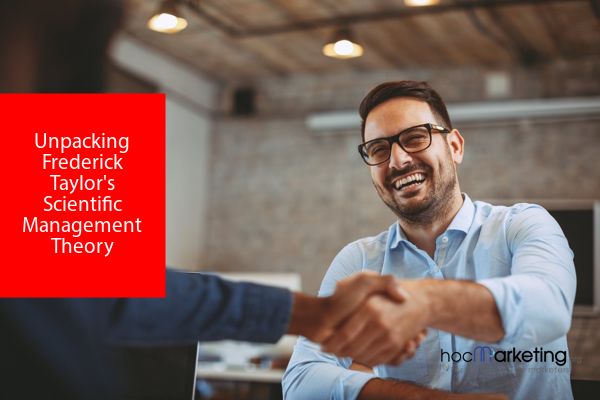
Unpacking Frederick Taylor's Scientific Management Theory
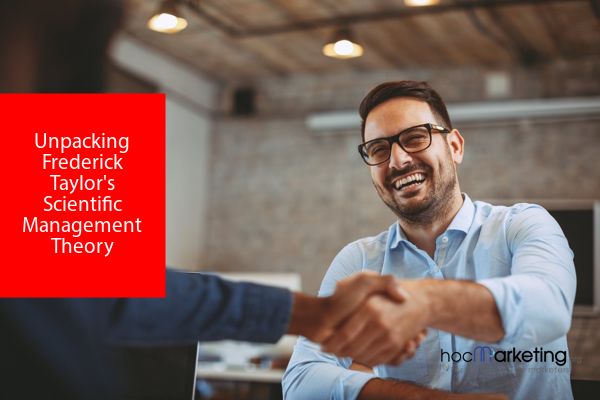
Frederick Taylor's Scientific Management Theory revolutionized the world of business in the early 20th century With a focus on increasing economic efficiency, Taylor's tenets emphasized standardization, time and task education, and selecting the right resources However, critics dubbed it the Scientific system of sweating due to its intense focus on productivity
Imperialism had peaked just before the onset of World War I, with a strong emphasis on maximizing economic output from existing resources as new colonies became scarce. The majority of colonies were under European control and the struggle to conquer territories resulted in two world wars and subsequent limitations on the free movement of people and goods across the globe. In order to thrive, entrepreneurs recognized the need to achieve greater results with fewer resources.
Running faster to stay in the same place
In the face of fierce competition and declining demand, business owners often found themselves struggling with slow growth. To overcome this challenge, they turned to scientific management theories that emphasized efficiency and dedication from employees. However, this approach typically involved a top-down management style with limited feedback from lower levels and a flow of information primarily from the top.
How Scientific management theory gained momentum with the passage of time!
Frederick Taylor's initial introduction of the theory was called shop management or process management. He was motivated to propose this theory after observing his colleagues consistently performing at less than one-third of their potential each day. To rectify this, he suggested implementing micro-motion studies with stop-motion cameras to standardize processes. This approach allowed for the application of scientific principles to management, answering questions such as "What is the optimal time for task completion?" and refining the principles of scientific management theory.
The theory's principles were initially implemented in factories and later adapted for the advancement of industrial psychology. Frank .B. Gilbreth (1868-1924) and Harrington Emerson (1853-1931) were among the notable figures who contributed to refining the theory. They strongly believed that public sector organizations could significantly benefit from employing the theory's principles, which could result in substantial cost and time savings. Taylor's recognition of the potential for workers to triple their output on the shop floor through time and motion studies, coupled with micro-motion studies utilizing stop-motion cameras, led to the further development of industrial psychology as a discipline.
1) Basic TENETS
Taylor's principles of scientific management gained popularity among intellectuals and lawyers who argued that implementing time and motion studies, using stop-motion cameras, could save thousands of dollars each day in state-run corporations by calculating the maximum time needed to perform each job. This approach could then be used to monitor the performance of employees in manufacturing and mining sectors. However, workers involved in mass production of goods vehemently opposed the implementation of this theory.
Frederick Winslow Taylor is widely regarded as the pioneer of this theory, and he collaborated with several other management experts to establish four fundamental principles. The initial and most crucial principle was identifying the most efficient method of performing a task.
Selecting first-class men or an A team to do the job.
Pay per piece in order to avoid leakages and wastages.
Outlining the basic duties of the management
Each of these tenets had to be adhered to strictly in order to achieve the goals of the organization.
2) Salient features
Managers plan on desk and workers execute the plan is the sub-text of the scientific management theories. This theory gained prominence as it synthesizes and analyzes workflows.
Business owners were faced with the challenge of improving economic efficiency in order to stay competitive with other industrialized powers. This led to a need to do more with less. With the introduction of scientific management theories, labor productivity skyrocketed. This was due to the application of science to the engineering of processes and management, marking a significant turning point in the way businesses operated.
3) Standardization
This is the first and foremost principle of the scientific management theories that refers to the speed and rate at which work needs to be done.
The demand for precision in manufacturing increased as the use of internationally recognized equipment and tools became more common. Consumers now expect products that meet strict quality control standards, leading to a greater emphasis on accuracy and consistency in production processes.
4) Time and task education
The purpose of these studies was to identify optimal work methods. This approach proved particularly valuable for industries that required identical, high-speed production of products. By utilizing stop motion cameras, researchers could accurately measure the time required to produce a single unit, accounting for factors such as power outages and inclement weather. The resulting ideal completion time was then communicated to the entire organization as the standard to strive for.
5) Higher emphasis on selecting the right resources
The hiring process of top companies is considered a cultural touchstone, and for good reason. These companies are known for their rigorous recruitment methods, which aim to identify candidates with the potential to thrive in the ever-evolving market. The selected resources are expected to deliver innovative solutions that can outperform and outshine the competition, ensuring long-term success for the company.
6) Impact of management
The concept that emerged during the post-World War 1 period had a significant influence on business conversations. This was a time when countries such as America were enjoying remarkable economic growth thanks to free trade, before the onset of the Great Depression in 1929.
As Russia embraced Communist principles, it began to emerge as a military and economic powerhouse. Meanwhile, other European nations were also navigating their own growth paths, with some adopting communism and others capitalism. This eventually led to the outbreak of the Second World War. The scientific management theories gained immense popularity during this time, with even Vladimir Lenin acknowledging it as the most widely discussed topic in the European business landscape. Though newer theories emerged and the original theory became outdated by 1930, its influence continued to shape the thoughts and actions of management experts and business leaders of the time.
Conclusion: “Scientific system of sweating”
Critics of the theory coined the term "scientific system of sweating" due to its applicability in blue-collar industries such as manufacturing and mining, where physical labor is more common than in white-collar and pink collar jobs. Despite this criticism, the principles and skills generated by the theory continue to be utilized in management today.
Analysis
Synthesis
Logic
Rationality
Empiricism
Work ethic