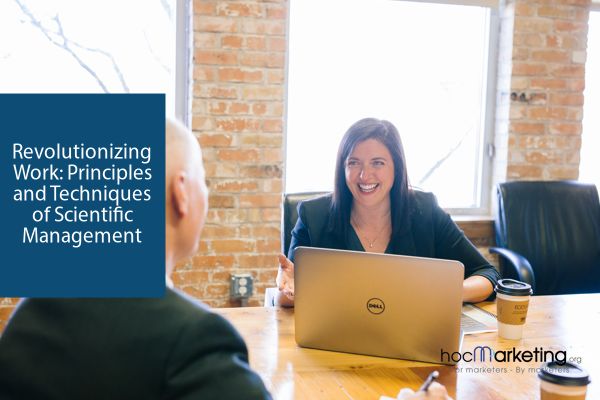
Revolutionizing Work: Principles and Techniques of Scientific Management
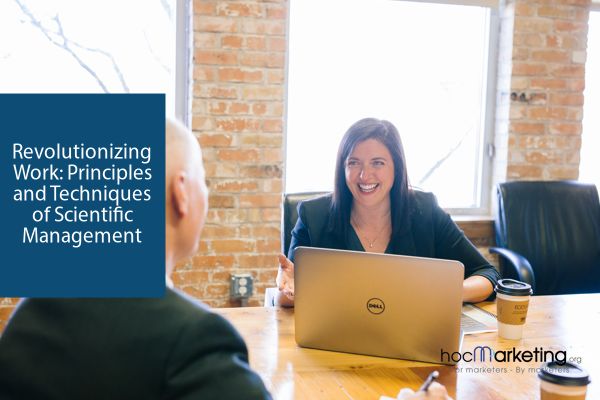
Frederick Taylor's Scientific Management revolutionized workplace efficiency Using principles such as science over tradition, worker job match, and work delegation, Taylor's techniques included standardization, simplification, and the scientific study of work Despite criticism, his methods paved the way for modern management practices
Frederick Taylor, a mechanical engineer at a steel corporation in Philadelphia, is credited with developing the principles of scientific management. Through his observations of workers on the floor, he sought to find ways to improve efficiency in task performance. This led to the development of time studies, activity analysis, and methodology studies, which are considered the foundation of Taylorism.
History of Scientific Management by Frederick Taylor
In 1909, Frederick Taylor introduced the principles of scientific management, advocating for the optimization and simplification of job tasks to boost productivity. He also emphasized the importance of positive relationships between managers and workers to achieve greater productivity, a departure from previous business practices. Prior to Taylor's ideas, factory managers had little to no interaction with workers, who were left to their own devices to complete tasks without standardized protocols or incentives beyond job security.
Taylor believed that fair compensation was a crucial factor in motivating workers, leading him to introduce the concept of a fair day's pay for a fair day's work. As a mechanical engineer, he was passionate about maximizing work efficiency and conducted numerous experiments in his workplace at US Steel manufacturers. Some of his most well-known experiments involved developing a shovel that enabled workers to work for multiple hours without fatigue and identifying efficient ways for bricklayers to lay bricks using different motions.
Studies conducted by Taylor revealed that some individuals were able to work more efficiently and effectively than others, leading to the conclusion that managers should focus on hiring the right people for the right job. This realization became a crucial component in the development of workplace efficiency, alongside Taylor's contributions to time and motion studies. As a result of his research, Taylor established four fundamental principles of scientific management, which are commonly referred to as Taylorism.
Principles of scientific management
Following four principles of Taylor’s scientific management:
1) Science over tradition:
Taylor advocated for the use of the scientific method over relying on rules of thumb or common sense when studying work processes and determining the most efficient way to perform tasks.
2) Worker job match:
Workers should be assigned jobs based on their motivation and capability, rather than randomly assigning them to any job. This approach ensures that workers are able to work at their maximum efficiency and contribute to the success of the company.
3) Supervising:
The work performance of the workers should be monitored often and instructions should be provided to them along with supervision so that it increases the efficiency of working.
4) Work delegation:
Allocate the work between the workers and their managers so that the workers can perform efficiently and the managers can use the time in order to plan and train accordingly.
Meaning and explanation | Scientific Management
1) Science over tradition
In many organizations and factories, it is often observed that certain rules, which were originally meant to be temporary solutions for specific problems, turn into permanent practices over time. Despite the fact that these solutions may not be the most effective or scientifically sound, they are still deemed as viable due to their previous success in solving the same problem. As a result, these ad hoc solutions become rules of thumb that are routinely applied whenever the same problem arises.
However, relying on such habits or common sense is not a sustainable or optimal approach to problem-solving, as pointed out by Frederick Taylor. Instead, a more methodical and scientific approach is necessary to truly address and solve the problem at hand.
We recommended utilizing a rigorous scientific approach to analyze the work at hand. Additionally, we proposed exploring more efficient methods of completing the tasks to maximize productivity within the given timeframe, rather than relying on conventional methods.
2) Worker job match
In the past, job assignments in organizations or factories were often made without considering whether a worker was physically and mentally capable of performing the job. However, Taylor advocated for a system where workers are matched with jobs based on their skills, resulting in increased efficiency and skill development. This approach also leads to higher motivation levels and greater job satisfaction among workers.
3) Supervising
In the past, there was a significant disconnect between workers and their managers. Managers would simply provide briefings on tasks and responsibilities without any real interaction during the work process.
The managers held themselves above interacting with workers, believing it could hinder their own efficiency. However, Taylor suggested that monitoring employee performance and providing guidance could ultimately improve productivity. By providing clear instructions and supervision, managers can fine-tune the output of workers, ensuring continued success.
4) Work Delegation
While the delegation of authority concept was introduced after Taylor's time, he is recognized for laying the foundation for work delegation. Taylor suggested that tasks should be assigned between employees and their supervisors.
Educating the workforce can greatly benefit managers by enabling them to devote more time towards training and planning for their employees. As a result, workers are able to perform their tasks more efficiently, leading to increased productivity and growth for the company.
Techniques of scientific management
There are 6 different techniques of scientific management which are as follows:
1. Functional foremanship
Taylor introduced the concept of functional organization, which emphasizes specialization and maximizes the use of experts and their skills. Each expert is responsible for a specific portion of the task, which is further divided into smaller parts.
The functional organization was founded on the principle that individuals should be assigned as many tasks as possible, resulting in increased work efficiency and reduced learning time. Additionally, the approach advocated for individuals to specialize in a single function whenever feasible, which would enhance their productivity and reduce the overall time required to complete tasks.
Taylor further suggested that the division of the work of factory manager should be made into two sub-departments:
A) Planning department
B) Production department
There should be four experts in each department and this should help the department to do the function more efficiently.
A) Planning department specialists
The role of a route clerk involves organizing the sequence of work and ensuring that it passes through all necessary stages before finalization. They are responsible for determining which tasks should be prioritized and where they should take place.
The Instruction Card Clerk is tasked with creating and distributing instruction cards to team leaders and bosses in charge of specific teams. These cards contain vital details such as the work's nature, standard procedures, materials required, and machinery used during the process.
The Time and Cost Clerk holds the responsibility of determining the start and end time of a specific task. Additionally, they are accountable for estimating the required time and cost for the completion of the work.
4) Discipline officer
Is the person who ensures that all of the work that is allocated to the workers is performed in a disciplined manner.
B) Production department specialists
The workers are categorized into two groups based on control. One group is led by a team leader, also known as a gang boss, who is responsible for ensuring that the machines and workers are compatible to optimize production and material availability.
The speed boss plays a crucial role in ensuring that all tasks are completed at the expected pace. If any delays or inefficiencies are identified, the speed boss investigates the root cause and suggests solutions to improve efficiency.
3) Repair boss
As the name suggests the primary function of the Repair boss is to keep the tools and the pieces of machinery in working conditions.
The role of an inspector involves inspecting the products and comparing their quality against a standardized form. Any discrepancies or gaps identified are noted and actions are taken to rectify the issue. Ultimately, it is the inspector's responsibility to ensure that the final product meets the required standards.
2. Work Standardization
Using standardized guidelines for work allocation can ensure consistency and efficiency in completing tasks. This not only benefits the worker by providing clear expectations, but also the organization by maximizing productivity.
1) Standardize materials
The quality of the finished goods is heavily dependent on the quality of the raw materials provided. It is imperative that only high-quality raw materials are used in production to ensure that the end product meets the desired standards. Using substandard raw materials will only result in a product that falls short of expectations. Quality control starts at the very beginning of the production process with the raw materials selection.
2) Standardization of tools and machiner
To ensure efficient production of finished goods, it is crucial to have an adequate supply of machinery and tools. By standardizing the machines used, errors caused by workers can be reduced, ultimately leading to faster completion of work.
3) Standardized methods
Efficiency can be improved by implementing standardized methods for completing tasks. By ensuring uniformity in the techniques used to perform work, tasks can be completed more quickly and efficiently.
4) Standardized working conditions
The working conditions have a significant impact on the productivity of employees. When working in an environment with standardized conditions, it is important to ensure that the ventilation, temperature, lighting, and cleanliness are appropriate for the job requirements.
3. Simplification
Eliminating extraneous features, varieties, or sizes is essential for optimizing efficiency. For instance, a shirt manufacturer may only need sizes ranging from 10 and up, rendering sizes 4, 5, 6, and 7 unnecessary.
For adults, shirt sizes typically range from 36 to 44, with a difference of 2 between each size (36, 38, 40, 42, and 44). It would not be practical to include sizes such as 36.5 or 36.6. Simplification is often used to streamline production and decrease labor costs through work specialization.
4. Scientific Study of Work
Prior to any organizational activity, it is crucial to conduct a thorough analysis. By doing so, the quality of output can be enhanced while minimizing costs. Taylor's studies have identified several key areas to focus on.
A) Method Study
Optimizing processes is about finding the most effective and efficient way to perform a task or activity. This involves utilizing tools such as process charts and operation research to analyze and improve the process. The ultimate goal is to reduce production costs while simultaneously increasing the level of quality and satisfaction for consumers.
B) Motion Study
The aim of this research is to analyze the movements executed by both machines and workers during job tasks. To achieve this, a movie camera can be utilized to record the actions performed. The ultimate goal of this study is to identify and eliminate any unnecessary movements that do not contribute to the completion of the task, thus reducing the overall time required to finish the job.
C) Time Study
Determining the standard time required to complete a job is crucial, and this is where the study comes in handy. By taking into account multiple experiences of the same work, the average time taken can be calculated to determine the standard time.
D) Fatigue study
Utilizing a stopwatch can aid in achieving the goals of the study, such as analyzing labor expenses, identifying the optimal number of employees needed, and selecting an appropriate incentive structure.
Rewritten fragment: The frequency and duration of rest intervals required to complete a job are analyzed in a fatigue study. Workers often feel refreshed after taking a break, which allows them to return to work at full capacity. The goal of the study is to maintain worker efficiency. However, long working hours and poor working conditions can lead to fatigue and unhappy relationships with superiors.
5. Differential piece rate or Differential Wage system
Taylor proposed a wage system to incentivize employees based on their productivity rather than the time spent on the job. This system involves two distinct rates of pay: a higher rate for workers who meet the required unit production within a set timeframe, and a lower rate for those who do not meet the required units.
This will keep the workers motivated and push them further to perform better.
6. Mental Revolution
The concept of a mental revolution involves a shift in the attitudes and perspectives of both employees and employers. According to Taylor, this change in mindset can lead to increased productivity and cooperation between the two parties.
Instead of engaging in conflict over profit distribution, Taylor proposed that employees and workers work together to increase profits. By doing so, they can achieve higher production and generate more revenue.
Criticism of scientific management
Frederick Taylor's scientific management theory posits that there is only one correct method to perform a task, a notion which has since been challenged by modern management techniques such as management by objective, continuous improvement, and business process reengineering. Furthermore, Taylor advocated for monitoring and controlling workers to enhance productivity, but research indicates that employees prefer greater autonomy and tend to react negatively to excessive boss intervention.
.
The concept of Taylorism is based on the idea that individuals should focus on their specific tasks and break down work into smaller components for maximum efficiency. However, modern management systems prioritize a more holistic approach to work, utilizing teamwork to increase productivity and efficiency. The belief is that teamwork fosters collaboration and the sharing of ideas, knowledge, and experience among workers, leading to better results.
While Taylor suggested separating mental and manual work, modern management recognizes the value of incorporating workers' ideas and knowledge into their practices. This promotes a sense of motivation and importance among workers, as they feel their contributions are valued and impactful. By prioritizing teamwork, organizations can create a culture of collaboration and continuous improvement, resulting in better outcomes for all involved.