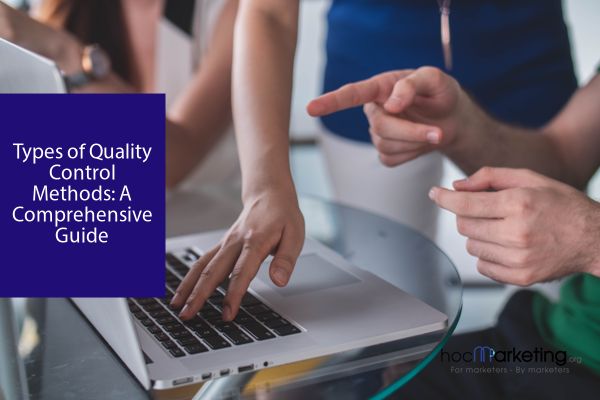
Types of Quality Control Methods: A Comprehensive Guide
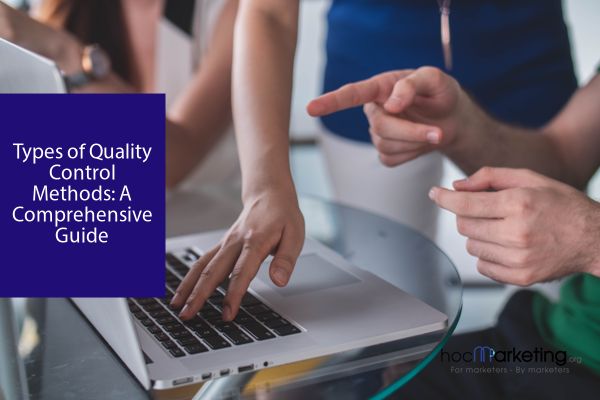
Quality Control entails utilizing management tools to effectively identify and solve work-related issues Discover the 7 types of QC tools including flow charts, check sheets, control charts, fishbone diagrams, histograms, Pareto charts, and scatter diagrams Implementing these tools can improve overall quality and productivity
Effective quality control is essential for ensuring that all products and services meet the required standards and specifications. It involves the use of various quality management tools to analyze and address work-related issues in a timely and efficient manner. By implementing a robust quality control process, organizations can minimize the risks of defects, customer complaints, and other quality-related problems. Ultimately, this can help to enhance customer satisfaction, build brand loyalty, and drive business growth.
The responsibility of ensuring that a company's products or services meet expected standards and specifications falls on the quality control department. They achieve this by utilizing appropriate QC tools. Quality control tools also play a vital role in project management, ensuring that the completed work aligns with the project's intended objectives. In this article, we will explore the various types of QC tools and their respective uses. Let's dive right in!
What are the QC Tools?
Quality control tools or QC tools are used to measure quality.
Quality can be measured through a variety of parameters such as performance, reliability, and ease of use. A product or service that meets the expectations and requirements of customers is considered to be of high quality. To measure quality, QC tools are utilized.
Effective monitoring and management of deliverable quality is crucial for any project's success. Quality control tools are essential in identifying and resolving quality issues, enabling the quality control team to gain a comprehensive understanding of critical issues, maintain consistent product quality, and implement practical and effective solutions.
What are the Types of QC Tools?
Dr. Kaoru Ishikawa, an engineering professor at Tokyo University, introduced the seven quality control tools (7 QC tools) in Japan. These tools have been widely recognized for their effectiveness in enhancing the quality of processes and products.
The tools analyze the production process, pinpoint any concerns, and offer effective solutions to prevent future issues. What sets these tools apart is their user-friendly design, making them accessible to anyone regardless of their analytical or statistical skills. Not only are they straightforward to use, but they also have a significant impact on fixing critical quality problems in products and services.
7 Quality Control Tools
1. Stratification or Flow Chart
: The seven quality control tools, initially introduced by Dr. Kaoru Ishikawa, are highly effective in identifying and addressing process and product quality issues. These tools include the cause-and-effect diagram, control charts, scatter diagrams, histograms, Pareto charts, flowcharts, and check sheets. By utilizing these tools, organizations can enhance their quality control processes and ensure customer satisfaction.By dividing the data into smaller groups, it becomes easier to identify patterns and trends. This allows for targeted improvements and adjustments to be made, leading to greater efficiency and productivity. Furthermore, the use of stratification in quality control helps to reduce the risk of errors and inconsistencies in data analysis. Overall, this tool is invaluable in ensuring high-quality performance and output in a range of industries and settings.
To get the best results from stratification, make sure to include which information about your data sources may affect your analysis results.
2. Check Sheet
A check sheet is used to collate, record, and analyze data.
It forms the basis for any problem-solving activity and is an essential step in the quality control process.
Data may be numerical, opinions, or observational.
3. Control Chart
The Shewhart chart, also known as a control chart, is used for monitoring performance and detecting variations in data points over time. It presents the collected data in a graphical format for easy interpretation.
The control chart showcases data trends over time and provides insights into the consistency or irregularities in data patterns. One of its primary purposes is to identify the root cause of process variations in the manufacturing process.
It helps identify when to take action to eliminate the random or unique cause of variations.
It helps to measure the process capability of the production process.
4. Fishbone Diagram or Cause and Effect Diagram
Fishbone is also called the cause and effect diagram.
By identifying the factors that lead to an effect, root cause analysis helps pinpoint the underlying problem that needs to be addressed. It accomplishes this by sifting through all potential causes and honing in on the most likely culprit, ultimately contributing to the resolution of the issue at hand. Brainstorming is a common method employed to identify potential causes.
The fishbone diagram provides a systematic approach to identifying potential causes of a problem. By categorizing causes and sub-causes into six main groups - machines, measurements, materials, personnel, environment, and methods - the diagram facilitates a thorough analysis and efficient problem-solving process.
5. Histogram
Utilizing a histogram is an effective method for displaying the frequency distribution of data in a clear and concise manner. This allows for the easy identification of areas that may require improvement within a given process, streamlining the overall improvement process.
A histogram is essentially a bar graph that depicts groups of data and the frequency of data in each group. The height of each bar corresponds to the frequency of the data, making it an effective visual tool for displaying frequency distributions.
This tool helps categorize the frequency of your data into age, days of the week, or any other data that can be represented chronologically or numerically.
6. Pareto Chart
Pareto chart is based on the 80-20 principle.
According to the 80-20 rule, 80 percent of the problems are caused due to 20 percent of the few major causes.
The crucial factors, known as the vital few, are responsible for the majority of problems according to the Pareto principle. The remaining 20 percent of issues are attributed to a plethora of minor causes, also known as the trivial many. To visually display this data, a Pareto chart utilizes both bar and line graphs. The bars are arranged in descending order to represent individual values, while the line graph depicts the total.
The Pareto chart helps identify the importance of different parameters and aids in concentrating your efforts on those factors that significantly impact the process.
7. Scatter Diagram
The scatter diagram is a valuable tool for quality assurance professionals in identifying cause-and-effect relationships between two variables. It visually displays the relationship between two sets of numerical data, providing insight into the correlation between the two.
The scatter diagram is an effective tool for quality control purposes as it can determine whether there is a positive or negative correlation between two variables. This helps to identify potential causes of defects in quality, such as personnel, activity, and other variables.
Why Should you Use the 7 QC Tools?
These are a few reasons why the seven quality control tools have become essential in quality control circles.
Encourages problem-solving and improvement in the process
Simple to use and powerful.
Scientific and analytical approach to problem-solving
Each tool is different and facilitates different ways of problem-solving.
Easy to use, understand, and communicate.
Final Thoughts on Quality Control!
Utilizing the seven quality control tools has made identifying the root cause of issues more straightforward and efficient, leading to more streamlined and effective solutions. Familiarity with these tools is essential for any organization focused on maintaining high quality standards in today's competitive environment.
In conclusion, we welcome your thoughts on the significance of providing training on the 7 QC tools within an organization. The versatility of these tools allows for their application in various problem-solving situations, making them a valuable asset to any team.