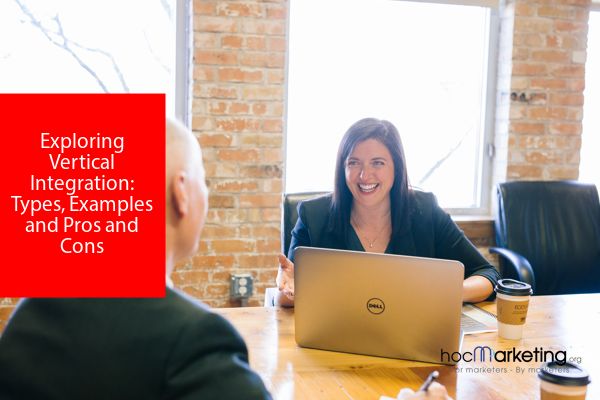
Exploring Vertical Integration: Types, Examples and Pros and Cons
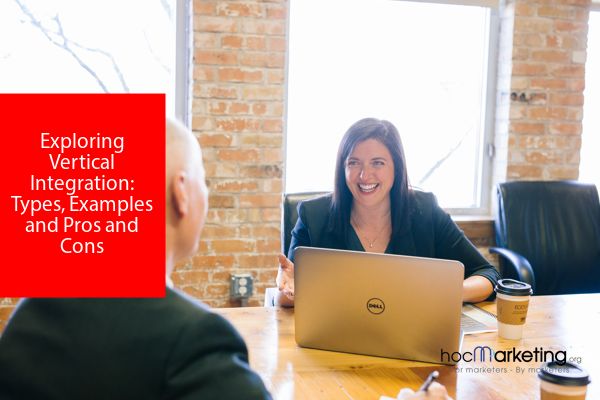
Vertical integration is a strategic move made by companies to gain better control over their supply chain It involves either backward or forward integration, or a balance of both There are advantages and disadvantages to integration, but it can lead to greater efficiency and profitability
Definition
Vertical integration is a strategic approach that companies adopt to enhance their control over the supply chain and achieve a more streamlined, effective, and well-regulated supply chain. The process involves the parent company, along with its suppliers and customers.
What is Vertical Integration?
Suppliers, who provide the materials, are located upstream and have been known to be dishonest. On the other hand, customers are located downstream and may also have questionable practices. Vertical integration offers the option to integrate with either the upstream suppliers or downstream customers.
In order to effectively manage its supply chain, any industry must consider the implementation of Vertical Integration as a strategic approach. This involves making important decisions regarding the company's focus and approach, such as whether to have a singular process for a specific industry or a multi-pronged approach for different industries. For instance, an automobile manufacturer must not only produce the vehicle, but also provide for repairs and maintenance. Conversely, a biscuit maker may opt to solely focus on the production process. Vertical Integration is typically decided at the corporate level as part of the overall strategy for the organization, including the type of integration to be utilized.
Types of Vertical Integration
There are three types of vertical integration, each of which is explained below.
1) Backward vertical integration
To delve into this topic, let's examine TAURON Group, one of Poland's most influential companies. As a major player in the energy market of Central and Eastern Europe and one of the largest companies in Poland, TAURON Group operates across all major energy sectors, including coal mining, electricity and heat generation, distribution, and supply. TAURON Polska Group, the country's largest distributor and retailer, is also the second-largest domestic energy producer.
2) Forward vertical integration
TAURON Group's acquisition of a coal production company exemplifies the benefits of backward vertical integration. By acquiring their vendor, the company was able to increase stability and revenue. This management strategy of tying up with vendors for better efficiency and control is commonly referred to as backward vertical integration. The outcome of this approach is generally improved margins and stability for the company.
Magazines that offer direct subscriptions to readers are an example of forward vertical integration, where intermediaries are eliminated and companies interact directly with their customers. For instance, EAM Publications, a publishing and distribution company in Tanzania, has implemented forward vertical integration by establishing its own distribution centers. As a result, EAM Logistics enjoys a competitive advantage in terms of pricing and quality control, as it can provide published materials directly to end customers without any intermediaries.
3) Balanced
The third type of vertical integration involves a combination of backward and forward integration. As we saw with the Tauron group example, backward integration involves owning and controlling the suppliers of raw materials or components. However, if Tauron were to directly reach out to end customers and provide electricity without any intermediaries, they would also achieve forward integration. This would result in the company integrating with both vendors and customers, covering both the upstream and downstream verticals. With such a strategy, Tauron can improve its core competencies, achieve better profit margins, and ultimately strengthen its market position.
Example of Vertical Integration
Despite the numerous benefits of vertical integration, many companies still struggle to adopt this concept. One major obstacle is the lack of expertise and resources. For instance, pursuing forward vertical integration may require the construction of a warehouse or storage room, as well as hiring additional employees to manage the new facilities. Additionally, employees may need to undergo costly training to acquire the necessary skills and knowledge to perform the newly integrated tasks.
Vertical integration in the automotive industry is demonstrated in this image. Car manufacturers such as Tesla exhibit both forward and backward integration. In order to acquire the latest equipment, Tesla employs backward integration with its suppliers, distributors, and commodity producers such as car battery and parts manufacturers.
Advantages of Integration
Tesla takes a proactive approach in working with its corporate customers, bulk buyers, car importers, and garage owners to ensure a seamless after-sales service and availability of spare parts. This not only benefits the customers but also strengthens the overall product offering of any automobile manufacturer.
Improved Quality – By implementing an integrated supply chain system, the quality of the company's supply also improves.
Enhanced Coordination – The utilization of advanced technological software enables better coordination within the supply chain.
.
Improved Efficiency – A well-managed supply chain leads to improved efficiency, reducing costs and increasing profits for the company.
Customer Satisfaction – A robust supply chain ensures timely delivery of products, meeting customer demands and increasing customer satisfaction.
Risk Management – A strong supply chain can help mitigate risks such as supply disruptions, quality issues, and compliance failures, protecting the company's reputation and bottom line.
Innovation – An efficient supply chain can also enable innovation by allowing companies to quickly adapt to changing market trends and customer demands.
Collaboration and Partnerships – A well-functioning supply chain requires collaboration and partnerships with suppliers, distributors, and other stakeholders, leading to mutually beneficial relationships and increased profitability.
Preparation for Emergencies – An integrated supply chain can be better prepared for emergencies as compared to a supply chain that is non integrated.
Disadvantages of Integration
Without proper management, integration can lead to more problems than benefits for the company. Additionally, improved coordination may require increased investments in technology and integration, resulting in higher costs and potentially impacting margins.
Fragment 16: This emphasizes the importance of maintaining quality throughout the supply chain as the involvement of multiple parties can potentially affect the regular maintenance and deliverable quality. Furthermore, failure of one part can have a detrimental effect on brand reputation, highlighting the need for a robust supply chain management system.